Internet of Things (IoT)
Un œil artificiel et intelligent pour détecter les défauts
3 juin 2019
Categorized: Industrie | Intelligence Artificielle | Internet of Things (IoT)
Share this post:
Destiné aux professionnels de la qualité, en particulier sur les lignes de production, Visual Insights vise à améliorer le contrôle visuel humain grâce à l’intelligence artificielle.
Quoi de pire pour un fabricant que de laisser passer sur ses lignes de production un objet comportant des défauts, et qui sera toutefois commercialisé ? Le client le renverra et l’entreprise devra le remplacer. Bien sûr, des contrôles visuels sont effectués : composants au bon endroit ; boulons correctement vissés ; couleur uniforme. Ce sont des êtres humains qui repèrent ces défauts visuels. Au milieu d’une chaîne robotisée, des caméras intelligentes peuvent trouver leur place. C’est ce que propose IBM avec Visual Insights.
Les premiers systèmes d’inspection visuelle automatisée sont apparus dans les années 90. Ils étaient basés sur des méthodes de traitement d’image, mais avaient des limitations assez bloquantes : ils étaient très sensibles aux changements d’éclairage, aux vibrations sur les chaînes de production, aux angles de prise de vue. L’avènement de technologies telles que deep learning permet maintenant d’avoir des algorithmes de reconnaissance visuelle beaucoup plus fiables et performants, à l’image de ceux présents dans Visual Insights. L’objectif est de donner aux fabricants la possibilité d’utiliser ces algorithmes de deep learning dans le cadre de l’inspection et du suivi de la qualité des produits finis : téléphones, téléviseurs, voitures, les applications ne manquent pas. Visual Insights propose un algorithme de détection sur images, mais pas seulement : il accompagne le responsable de production dans ses tâches journalières pour valider le niveau de qualité de ses produits. Visual Insights s’appuie sur des briques open source qu’IBM a intégrées dans une boîte à outils avec une interface spécifique pour les responsables et inspecteurs des lignes de production. La solution a été optimisée afin de limiter les faux négatifs (aucun défaut identifié dans l’image, alors qu’il en existe).
Entraînement obligatoire
De la même façon que les inspecteurs doivent exercer leur œil pour repérer les défauts, Visual Insights doit être entraîné. Cette phase consiste à « nourrir » l’algorithme avec des images (quelques centaines) des objets, avec et sans défaut. Une série d’images supplémentaires peut être générée artificiellement (phase d’augmentation), en faisant varier l’exposition, le contraste, l’orientation, etc. Deuxième étape, un modèle est créé et testé, ce qui prend de quelques minutes à quelques heures suivant sa complexité et le nombre d’images fournies. Plusieurs cas d’utilisation sont envisageables.
Le premier, le plus simple, consiste en une classification des images en fonction des défauts possibles. Deuxième cas, l’algorithme va devoir identifier tel ou tel défaut dans une image, par exemple, des rayures ou des chocs sur une portière de voiture. Dans ce cas, le logiciel ne se contente pas de classer l’image (avec ou sans défaut), mais va être capable de repérer une rayure en bas à gauche de la portière. Le modèle peut ensuite être mis en production. Le système de visualisation permet une détection plus rapide que l’être humain (de l’ordre de 20 %) et plus performante (en détectant des défauts presque invisibles à l’œil nu). Mais le logiciel ne travaille pas tout seul : le superviseur doit contrôler que l’algorithme effectue un nombre d’erreurs acceptable, et ne dévie pas trop du modèle initial au fil du temps. Pour ce faire, l’inspecteur a accès à un portail où il peut contrôler les classements effectués par l’algorithme et les corriger éventuellement (le logiciel apprenant en continu). Ce portail est également accessible au data scientist si l’entreprise en a un, lequel peut créer ses propres modèles et les importer dans Visual Insights. IBM propose des modèles préconfigurés et aide si besoin l’entreprise dans la phase initiale d’apprentissage.
Une architecture ouverte
Visual Insights s’appuie sur un serveur central hébergeant le moteur d’apprentissage et des serveurs dédiés qui effectuent le classement. L’architecture est ouverte et fonctionne intégralement dans le cloud, en mode hybride (apprentissage dans le cloud et serveurs dans l’entreprise pour le scoring) ou entièrement on-premises. Les performances de l’outil sont assurées par une déportation des calculs sur des serveurs en configuration Edge, pouvant fonctionner en clusters. Les premiers clients de cette solution sont dans le secteur de l’automobile (détection de défauts sur la peinture ou les sièges), de l’électronique grand public (détection de rayures sur l’écran d’un téléviseur) et du textile (défauts sur le maillage).
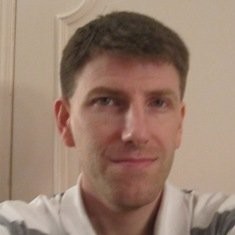
Principal Technical Sales Consultant – Watson IoT
IBM, avec ses modèles phares Granite, a été désignée comme « performer » dans le rapport de Forrester « The Forrester Wave™ : modèles de fondation d’IA pour le langage, Q2 2024 »
Alors que les entreprises passent de l’expérimentation de l’intelligence artificielle générative (IA générative) à la production, elles recherchent la bonne option en matière de modèles de fondation composée d’un mélange optimal d’attributs qui permettent d’obtenir une IA générative fiable, performante et rentable. Les entreprises reconnaissent qu’elles ne peuvent pas faire évoluer l’IA générative avec des […]
La robotique humanoïde et l’IA incarnée s’apprête à changer le monde !
Qu’on en ait peur ou qu’on en rêve, la robotique humanoïde a connu une évolution fulgurante ces deux dernières années. Ces robots représentent l’incarnation de l’IA dans notre monde physique, et ce via un facteur de forme qui lui est déjà parfaitement adapté : la forme humaine. Nous allons voir dans cet article ce qui […]
IBM et AWS offrent aux clients français de nombreuses technologies IBM sur la marketplace d’AWS pour répondre aux enjeux d’hybride Cloud et d’IA
Dans un monde de plus en plus complexe, qui ne souhaite pas un peu de simplicité ? IBM et AWS permettent aux clients français d’acheter, de déployer et d’utiliser plus facilement les logiciels IBM achetés sur la marketplace d’AWS. Avec un portefeuille de 44 solutions IBM (dont 29 en mode SaaS) désormais disponibles et en […]